‘MS Plate Weight Chart in KG’ PDF Quick download link is given at the bottom of this article. You can see the PDF demo, size of the PDF, page numbers, and direct download Free PDF of ‘MS Plate Standard Size Sheet’ using the download button.
MS Plate Weight Chart PDF Free Download
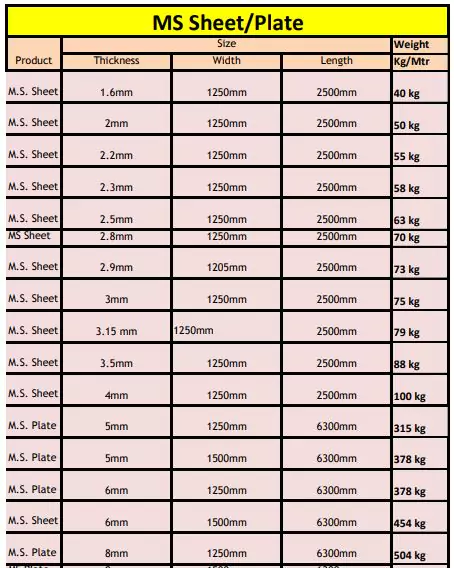
MS Plate Standard
Wide Range of Product Selection
Hot-Rolled Steel Sheets and Coils meeting a variety of standards ranging from mild steels to high-tensile strength steels are available.
Variable sizes of cut sheets, coils, and various surface finishes such as black finish, pickled finish and shot-blasted finish can be selected in accordance with your needs.
Consistent Quality
Products of consistent quality are manufactured under strict quality control, utilizing excellent equipment and techniques, and drawing on our wealth of experience.
Wide Variety of Sizes
Sizes are available from 1.2 mm to 25.4 mm in thickness and from 600 mm to 2180 mm in width.
Technical Service for Every Need
Consultation services regarding quality characteristics, applications, and processing methods of our products, and more are thoroughly provided by the technical service divisions of the headquarters and local offices.
Utilizing our excellent manufacturing equipment and honoured technology, supported by our rich experience and never-ceasing endeavour of development, NIPPON STEEL manufactures a wide range of Hot-Rolled Steel Sheets and Coils in accordance with Japanese Industrial Standards (JIS), the standards of other countries, and our own strict standards.
Our Hot-Rolled Steel Sheets and Coils are applied to a wide range of applications such as automobiles, electrical appliances, construction materials, containers, and steel pipes, and receive high acclaim from our customers for their excellent quality.
We are committed to meeting our customer’s requirements of quality as well as on-time delivery and offer technical consultations and services for applications of our steel products.
We deeply appreciate your continued support and encouragement.
Continuous Casting from the Blast Furnace
Pig iron is formed by a chemical reaction of sinter and coke in the blast furnace.
Then, in order to meet our customers’ demand for viscosity and robustness, the pig iron goes through four processes: hot metal pretreatment, converter process, secondary refining process, and continuous casting to remove excess carbons and impurities for chemical refinement in order to produce an intermediate material known as “slab.”
Plating Finish
Hot-rolled sheets (pickled) are coated with oil for protection against rusting. The lubricating oil used in the forming process may also remain on the surface.
All traces of such oil and impurities present on the surface must be removed before beginning the plating operations.
Degreasing can be achieved by various methods, including those using emulsions, alkali cleaners, etc. Of these, alkali cleaning is most widely employed because of its economy and ease of handling.
The most commonly used alkali cleaners include caustic soda, carbonic soda and sodium silicate. Time, temperature, and agitation are the determining factors in degreasing.
A surfactant added to the solution usually improves the degreasing effectiveness.
Types of steel that contain a sizable amount of silicon can cause defective plating.
Please contact us as we have steels that are compatible with plating.
Antirust
In order to provide maximum protection against rusting and at the same time to facilitate degreasing, hot-rolled sheets are lightly and uniformly treated with an oil that is low in viscosity and easy to remove but still provides superior protection against rust.
Since the sheets are only lightly oiled, they may rust if left exposed for an unreasonably long time after unpacking.
Unpacked sheets, therefore, should be used without undue delay.
When production conditions make it necessary to keep the unpacked or fabricated sheets exposed for a certain period of time before painting or plating, the following precautions should be taken.
a. Since humidity of or over 70 per cent usually accelerates the formation of rust, sheets should be kept in an environment with less than 60 per cent humidity.
b. Air pollution also affects rusting. Hygroscopic substances such as hydrochloric acid gas, ammonium chloride gas and seawater salt particles accelerate rust even when humidity is 60 per cent or less or temperatures are above the dew point.
c. Dust and stains present on the surface tend to break the protective oil film, produce local galvanic activity with the base metal, and cause rust.
Author | – |
Language | English |
No. of Pages | 2 |
PDF Size | 1 MB |
Category | Charts And Sheets |
Source/Credits | 5.imimg.com |
MS Plate Weight Chart PDF Free Download